Independent further API development
MODERN INTEGRATION PLATFORM FOR HIGH DATA AVAILABILITY
Industry: Manufacturing
Technology: MuleSoft Anypoint Platform
Highlights
Roll Out and adjustments during live operations
Reduction in time and costs through rapid error detection
Challenge
The existing interface management solution no longer met the requirements of the customer, a Swiss-based manufacturer of electronic devices. To keep up with the growing complexity of the company, it needed to be replaced it with a more dynamic system.
Furthermore, it needed to offer user-friendly API management that would enable the IT department to develop and maintain interfaces, making them less dependent on external providers and allowing them to implement a more straightforward release policy when rolling out new objects.
When implementing the new solution, it was also essential to consider the new company guidelines and network structure resulting from the latest cyber security adjustments.
The goal is to integrate a modern API platform that supports and accelerates the digital transformation of business processes. This involves gradually migrating all relevant 1:1 interfaces to the new system and replacing them. The long-term goal is to bring all production sites worldwide onto one single ERP system and to introduce and implement standard procedures for processing templates and interfaces.
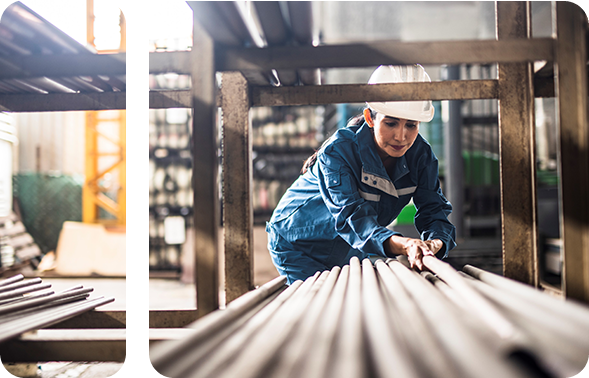
Solution
The MuleSoft Anypoint Platform was set up in an agile project setup and executed via the Kubernetes cluster in order to improve applications' availability, scalability, and recovery. As soon as the first interfaces were implemented, the solution's advantages, namely the architecture's simplicity and reusability, became apparent.
Based on this, another, more complex interface involving 12 APIs was implemented. The basic structure was set up by DIGITALL and later, it was adapted and further developed by the customer during the testing phase thanks to its user-friendliness. The rollout was carried out during live operations, so no maintenance time frames had to be taken into account.
The integration ensures the connection between the ERP and warehouse management systems and enables the transfer of master data and transaction data between the systems during material withdrawals. In addition, it is used to prepare and display image information for various purposes such as the newly developed web store, internal sales, and the production line and logistics.
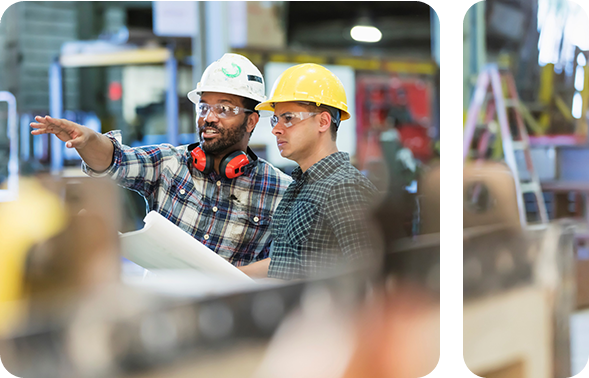
You have a question or a specific use case?
Write us a message and we'll be in contact with you to help your business find the right solution.